焊接品质检测案例1 焊道的形状检测
下面介绍利用高性能激光位移传感器进行焊接后的焊道外观形状(咬边、搭叠、余高不够等表面缺陷)检测案例。
案例1-1:激光焊道的2D截面形状检测
在焊接的后续工序中,目视进行全数检测时,不仅非常费时,同时也很难确保技能出众且有经验的检测员,可能会遗漏一些细微缺陷,出现人为失误,这是一个非常严峻的问题。此外,在使用视觉系统或传统红色激光位移传感器进行的焊接检测中,会因焊接焊炬的光或工件的漫反射光而发生误检测。*
与本公司LJ-G5000 系列产品的比较
利用“LJ-X8000系列”进行高速且稳定的截面形状检测
如果使用超高速轮廓测量仪“LJ-X8000系列”,就不会受到焊接车间的光学干扰影响,可高速且稳定地检测工件的截面形状,适用于各种形状的工件,因此可解决焊接的全数检测时发生的各种问题。
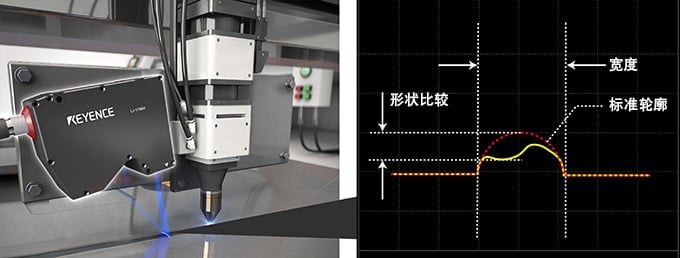
例如,在拼焊(TB)的激光焊接工序中导入“LJ-X8000系列”,可在不增加单件作业时间的前提下,追踪机器人的焊炬,在焊接后立即稳定地对焊道进行形状检测。利用最快64 kHz采样,即使在自动焊接时扫描头随焊炬快速并行移动,也可实现稳定的形状检测,可立即检测出焊接缺陷,将发生不良的可能性降低。
- 不同采样速度下形状检测的比较
-
传统的激光位移传感器:检测节距大,容易忽略突起部。*
与本公司LK-G5000 系列产品的比较LJ-X8000系列:利用高速采样的细微节距,不放过突起部。
- 可在各种测量模式下用于各种工件
-
“LJ-X8000系列”可指定16种测量内容和11种测量对象,共配备74种测量模式。利用丰富的测量模式,可对各种工件的焊接部、焊接焊缝进行形状检测。
-
- 高度
-
测量指定范围内的高度。
-
- 宽度、位置
-
根据指定条件,测量宽度和位置。
-
- 角度、交点
-
测量所检测的直线角度和交点位置。
-
- 标准轮廓比较
-
与注册的标准轮廓相比,测量高度差最大的部分。
-
- 高度差
-
测量参考点与测量点的高度差。
-
- 截面面积
-
测量距参考面的截面面积。
-
- 距离(点-点)
-
测量2点间的距离。
-
- 半径、中心位置
-
测量曲线形状的半径或指定点的中心位置坐标。
案例1-2:焊道的3D形状检测
在3D形状检测中,可对更多形状的焊接部进行检测,如仅凭2D截面形状数据无法检测出来的凹痕、咬边的容积、搭叠的体积、焊道表面的开裂、焊道弯曲(焊道歪斜、焊道错位)、焊道长度不良(坡口残留等)或电弧擦伤、溅射等。
利用“LJ-X8000系列”和视觉系统进行的3D形状检测
利用超高速轮廓测量仪“LJ-X8000系列”检测到的2D截面形状数据,生成3D形状并进行分析,实现精密的形状检测。
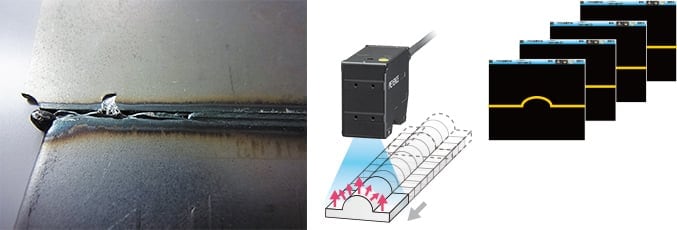
利用LJ-X8000获取焊道的2D截面形状数据
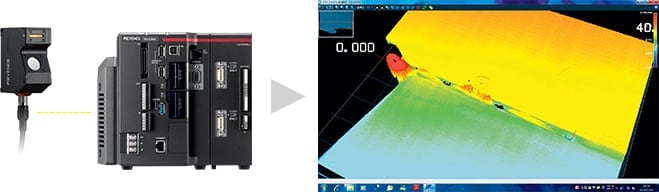
使用最大16284的截面形状数据,通过视觉系统生成3D形状
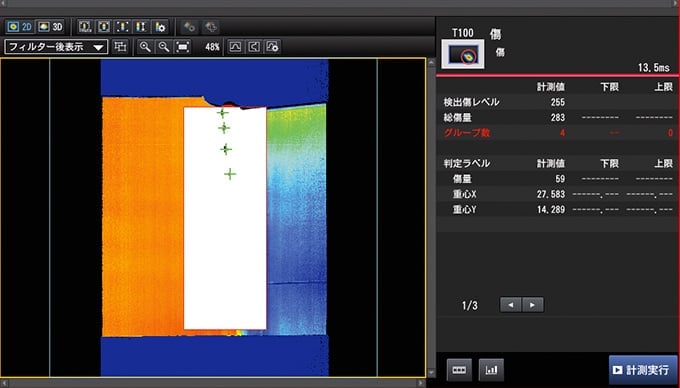
对焊道的3D形状进行分析,检测各种不良
- 借助3D形状检测实现的焊接部形状检测示例
-
凹痕、咬边的容积
搭叠、焊道的高度和体积
焊道表面的开裂、凹陷
电弧擦伤、溅射
焊道的弯曲、错位
焊道的长度
以上述内容为主,可对焊接部的各种形状不良进行在线检测。
搭叠或余高不够、坡口残留、电弧擦伤、溅射的3D形状测量示例
检测内容
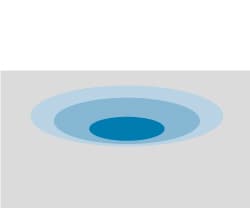
凹痕、咬边的容积
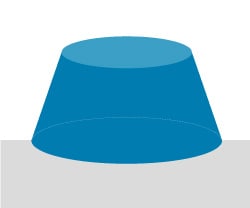
搭叠、焊道的高度和体积
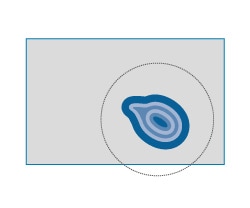
电弧擦伤、溅射
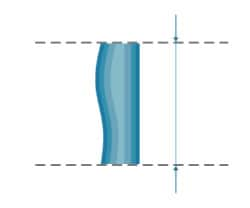
焊道的长度
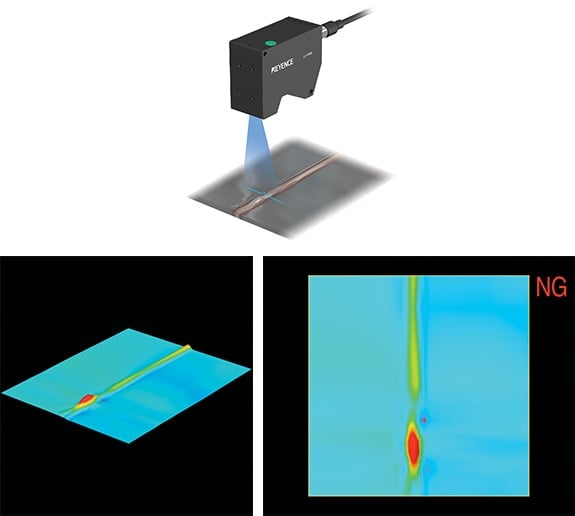
激光焊接余高不够(焊道凹陷)的3D形状检测和分析示例
检测内容
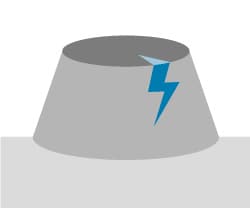
焊道表面的开裂、凹陷
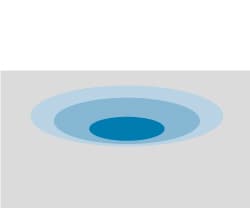
凹痕、咬边的容积
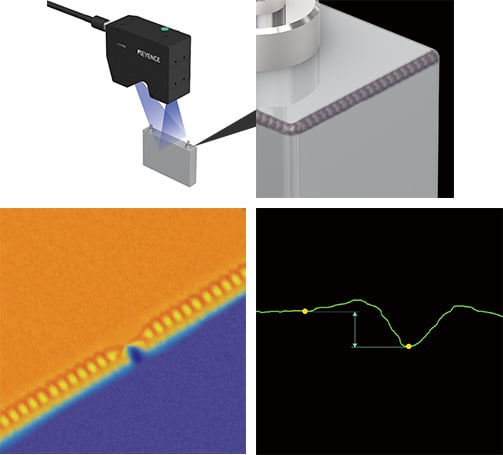
焊道弯曲(焊道歪斜、焊道错位)、搭叠的3D检测和分析示例
检测内容
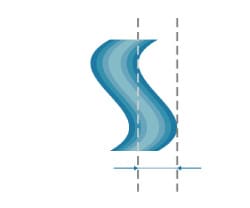
焊道的弯曲、错位
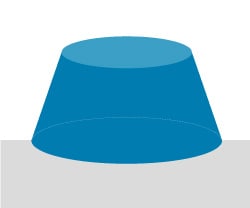
搭叠、焊道的高度和体积
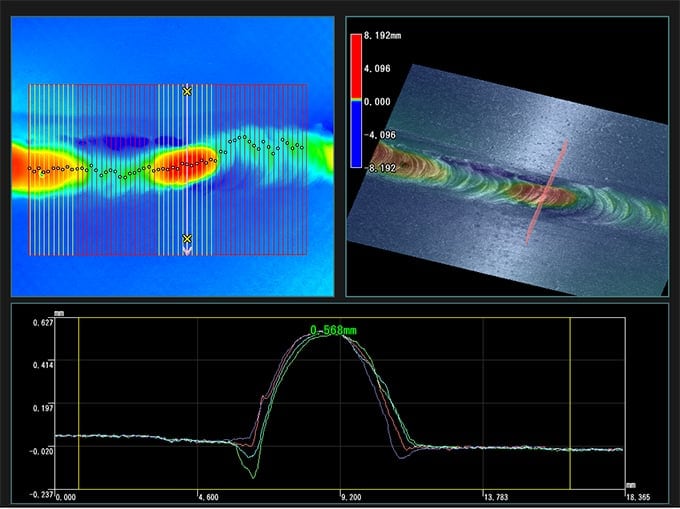